Comparison of PVD deposition methods
- gwj0606
- Aug 26, 2020
- 7 min read
Updated: Sep 4, 2020
A. What does PVD mean?
PVD (Physical Vapor Deposition) is a technology that uses physical methods to vaporize the surface of the material source into atoms, molecules or ions under vacuum conditions, and deposit a thin film with a special function on the surface of the substrate. PVD is mainly divided into three categories: evaporation, sputtering and ion plating.
B. Vacuum evaporation
Under vacuum conditions, the plating material is heated to evaporate or sublime, and the atoms or molecules of the material are directly formed into a film on the substrate. Several common vacuum evaporation techniques are introduced below:
1. Resistance evaporation
The evaporation coating technology using resistance heating evaporation source is generally used to evaporate low melting point materials, such as aluminum, gold, silver, zinc sulfide, magnesium fluoride, chromium trioxide, etc.; heating resistors generally use tungsten, molybdenum, tantalum, etc.
Advantage
Simple structure, low cost,
Disadvantage
The material easily reacts with the crucible and affects the purity of the film
Can not evaporate high melting point dielectric film;
Low evaporation rate
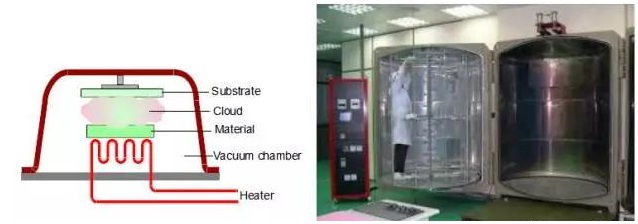
2. Electron beam evaporation
A technology that uses high-speed electron beam heating to vaporize and evaporate materials and condense into a film on the surface of the substrate. The energy density of the electron beam heat source can reach 104-109w/cm2, can reach 3000 ℃ or more, and can evaporate high melting point metals or dielectric materials such as tungsten, molybdenum, germanium, SiO2, AL2O3, etc.
There are two types of vapor deposition sources for electron beam heating: straight gun type electron gun and e type electron gun (also circular). The electron beam is emitted from the source, and the magnetic field coil is used to focus and deflect the electron beam to bombard and heat the film material.
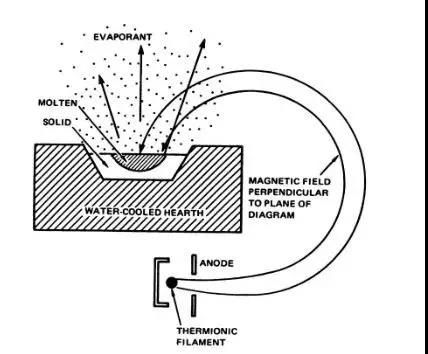
Advantage
Any material can be evaporated
High film purity
Act directly on the surface of the material, high thermal efficiency
Disadvantage
The electron gun has a complicated structure and high cost
The compound is easy to decompose when deposited, and the chemical ratio is out of balance
3. Laser evaporation
The method of using high-energy laser beams to evaporate materials to form thin films is generally called laser evaporation.
Advantage
High film purity
High evaporation rate
Especially suitable for evaporating alloys or compounds with complex composition, and the stoichiometric ratio of the film layer is consistent with the target material
Disadvantage
It is easy to produce small particles splashing, which affects the quality of the film.
4. Induction heating evaporation
A technology that uses high-frequency electromagnetic field induction heating to vaporize and evaporate materials to condense and form a film on the surface of the substrate.
Advantage
High evaporation rate, which can be about 10 times larger than resistance evaporation source
The temperature of the evaporation source is stable and splashing is not easy to occur
The crucible temperature is lower, the crucible material has less pollution to the membrane
Disadvantage
Evaporator must be shielded
High cost and complex equipment
C. Sputtering
In a vacuum, high-energy particles bombard the surface of the material so that its atoms gain enough energy to escape the surface and reach the substrate to deposite into a film.
Sputter coating is suitable for all materials (including high melting point), and has the advantages of strong adhesion, controllable composition, and easy mass production. The composition for sputter targets is quite abundant. As an example, QS Advanced Materials could supply a series of mixed oxide sputtering targets, which is very hard for evaporation processes. Also, the sputtering technique can be available for many kinds of substrates, including plastics and metal. Thus, it could be a very important branch of PVD process that could be applied in decoration fields.

1. Two-pole sputtering
A direct current high voltage is added between the target and the substrate, the gas between the plates (usually Argon) is ionized, and the high-speed charged ions bombard the surface of the target with sputtering coating technology. To maintain self-sustained discharge, the discharge gas pressure is generally as high as 10 Pa under the normal sputtering distance of several centimeters between the two electrode plates, which is detrimental to the sputtering efficiency and film quality. Therefore, DC sputtering mostly uses non-self-sustained discharge, that is, quadrupole sputtering with the thermionic emitter and auxiliary anode added, and the sputtering can be carried out at a low pressure of 10-1 to 10-2 Pa.
Advantage
Simple structure
Disadvantage
Only metal materials with good conductivity can be sputtered
Low sputtering efficiency
2. RF sputtering
A radio frequency power supply is used instead of a DC power supply, and a high frequency voltage is applied between the target and the substrate. During sputtering, the target will produce a self-bias effect (that is, the target will automatically be in a negative potential state) to maintain the sputtering of the insulated target . The commonly used frequency is about 13.56 MHz.
Advantage
Can sputter all materials, including conductors and insulators
High sputtering efficiency
Can be mass produced
Disadvantage
Radio frequency power supply has certain radiation problems
3. Magnetron sputtering
The working principle of magnetron sputtering is that under the action of electric field E, electrons collide with argon atoms in the process of flying to the substrate, causing them to ionize to produce Ar positive ions and new electrons; the new electrons fly to the substrate, Ar ions accelerate to the cathode target under the action of an electric field, and bombard the surface of the target with high energy, causing the target to sputter. In sputtering particles, neutral target atoms or molecules are deposited on the substrate to form a thin film, and the secondary electrons generated will be affected by electric and magnetic fields, resulting in a shift in the direction indicated by E (electric field) × B (magnetic field), referred to as E×B drifts, and its trajectory is similar to a cycloid. If it is a toroidal magnetic field, the electrons will move in a circular motion on the target surface in an approximate cycloid form. Their path of motion is not only very long, but also confined in the plasma region close to the target surface, and a large amount of ionization in this region Ar is used to bombard the target material to achieve a high deposition rate. With the increase in the number of collisions, the energy consumption of the secondary electrons is exhausted, gradually moving away from the target surface, and finally deposited on the substrate under the action of the electric field E. Since the energy of the electron is very low, the energy transferred to the substrate is very small, resulting in a low temperature rise of the substrate. Magnetron sputtering is the collision process between incident particles and target. The incident particles undergo a complex scattering process in the target, collide with the target atom, and transfer part of the momentum to the target atom, which in turn collides with other target atoms to form a cascade process. In this cascade process, target atoms near certain surfaces gain enough momentum to move outwards and leave the target to be sputtered.
Advantage
High film formation rate
Low substrate temperature
Good film adhesion
Large area coating can be realized
Disadvantage
The target material is not uniformly consumed, and the target material of magnetic material cannot be used
4. Reactive sputtering
The development of modern surface engineering increasingly requires the use of various compound films, and reactive magnetron sputtering technology is one of the main methods for depositing compound films. To deposit a compound film with multiple components, you can use a target made of compound material for sputtering deposition, or when sputtering a pure metal or alloy target, pass a certain reactive gas, such as oxygen, nitrogen, and reactively deposit the compound film. It is called this reactive sputtering. Generally, pure metal targets and reactive gases are easier to obtain high purity, so reactive sputtering is widely used to deposit compound films.
Advantage
(1) Reaction The target material (single-element target or multi-element target) and reactive gas (oxygen, nitrogen, hydrocarbon, etc.) used in magnetron sputtering are of high purity, which is beneficial to the preparation of high-purity compound films.
(2) By adjusting the process parameters in reactive magnetron sputtering, a chemically proportioned or non-chemically proportioned compound film can be prepared, and the film characteristics can be adjusted by adjusting the composition of the film.
(3) During the reactive magnetron sputtering deposition process, the substrate temperature rise is small, and the substrate is usually not required to be heated at high temperature during the film production process, so there are fewer restrictions on the substrate material.
(4) Reactive magnetron sputtering is suitable for the preparation of large-area uniform thin films, and can realize the industrialized production of single machine with an annual output of millions of square meters of coating.
Disadvantage
Prone to problems such as target poisoning and anode disappearance
D. Ion plating
Ion plating uses gas discharge to ionize gas or evaporated substances under vacuum conditions, and vaporizes the evaporated substances or their reactants on the workpiece under the bombardment of gas ions or evaporated substances. Including magnetron sputtering ion plating, reactive ion plating, hollow cathode discharge ion plating (hollow cathode evaporation method), multi-arc ion plating (cathodic arc ion plating), etc. Ion plating combines glow discharge, plasma technology and vacuum evaporation technology, which not only significantly improves the performance of the coating, but also greatly expands the application range of the coating technology. In addition to the advantages of vacuum sputtering, ion plating also has the advantages of strong film adhesion, good diffraction, and a wide range of materials that can be plated. Therefore, in recent years, it has developed rapidly at home and abroad. The basic principle of ion plating is to ionize metal or alloy vapor by means of a glow or arc discharge of an inert gas. Ion plating includes the heating, evaporation, and deposition processes of coating materials (such as TiN, TiC). When the evaporated coating material atoms pass through the glow zone, a small part of them ionize, and fly to the workpiece under the action of the electric field, and hit the surface of the workpiece with an energy of several thousand electron volts, which can penetrate the substrate to a depth of about several nanometers. , Thereby greatly improving the bonding force of the coating, and the non-ionized evaporation material atoms are directly deposited on the workpiece to form a film. The sputtering of inert gas ions and coating material ions on the surface of the workpiece can also remove contaminants on the surface of the workpiece, thereby improving the bonding force.
advantage
High deposition rate
Dense film
Good diffraction, strong ability to cover complex surfaces
Comments